The Electrification of Mining Vehicles
Business News • 3 min read • Aug 26, 2022 4:27:27 PM • Written by: Amelia Inskipp
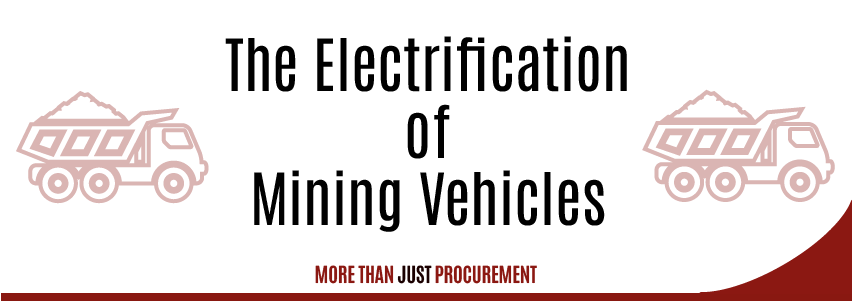
The Electrification of Mining Vehicles
For years, the mining industry (as well as many others) has relied on diesel to fundamentally power operations. However, these diesel-powered instruments, such as machinery and colossal trucks, are damaging not only to the planet but can also be extremely detrimental to the mine employees.
In a previous post, we spoke about the advancements the mining industry is taking to help reduce carbon emissions and new forms of technology which will be implemented to improve the output of these harmful chemicals. One of these was the introduction of battery-operated vehicles, and in this article, we will investigate the introduction of these vehicles further.
The number of electric cars on the world’s roads has tripled since 2018, with 16.5 million drivers choosing to swap to more eco-conscious vehicles. The demand for these vehicles is not slowing down any time soon, and other industries are now becoming more conscious of how business practices are taking a toll on the planet.
A trend in the mining industry is decarbonising mining operations, and a way companies are tackling this is through the electrification of haul trucks. Electric haul trucks are becoming so prevalent due to the amount of carbon that existing trucks emit.
Diesel-powered haul trucks are responsible for up to 80% of a mine's carbon emissions. An average mining truck burns roughly 300-400 litres of diesel every hour. Electric vehicles use a tenth of this amount has the potential to save 350 litres of fuel an hour. The toxins that diesel vehicles emit can also harm the workers due to the damaging mix of carbon monoxide and nitrogen oxide.
Not only do they generate an extreme number of pollutants, but they also emit an excessive amount of heat. Mines are high-risk temperature environments; some mines require intense ventilation, which could even include air-conditioning systems to create an able working environment. In a vicinity that is thousands of meters already underground, with little air circulation, these vehicles put an added strain on ventilation systems.
Electric-powered vehicles eradicate both options. They are a cleaner, cooler, and more efficient alternative to diesel-powered vehicles. Without the excessive amount of heat being produced, it drastically reduces the reliance on ventilation equipment. Electric vehicles also lose very little energy as they do not produce excess heat or noise, resulting in a cooler working environment.
A common misconception about electric-powered vehicles is that they are not as efficient as diesel-run vehicles. However, this is not the case. The battery ran vehicles can be more powerful than their diesel counterparts. As batteries develop more and become more adept, they can have double the horsepower, therefore having the ability to carry loads 10% faster. This will improve productivity as they have the ability to carry larger loads at a faster rate.
These machines are now being built and designed around batteries and electric motors. The batteries need to be re-charged more often than diesel engines would need refuelling. However, miners have found this particularly easy as they can be changed in as little as 15 minutes. With new technologies being built around the efficiency of replacing the battery, it eliminates the need for refilled trucks to make the long journey of travelling to the mine.
A downside to using electric vehicles causing mines to hesitate in implementing them is the upfront costs it causes as they are more expensive than diesel vehicles. Many mines have already invested a significant amount of money in the tools, and machines, so shifting all the existing machinery will require evening more funding. Therefore, the best place to introduce all-electric systems is a new mine. Transitioning is possible, but for a heavy diesel-reliant mine, the best approach is a gradual transformation. Electric vehicles have lower operating costs and a longer life span, therefore, in the long run they are more economical, even more so as they offset other costs such as ventilation requirements.
Moving toward electrification is the future of this industry which will be a long process, especially if mines are being redesigned around the new equipment rather than introducing them to new mines. A critical aspect which will spur change is the collaboration of mines working with each other. Some of the leading mining companies are already making these substitutions, spurring the confidence that other mines will need to acknowledge and accept the investment.
Now is the time for mining companies to realign their strategy and start to focus on decarbonising the way they operate. A way Storm Procurement is doing our bit is by committing to operating responsibly through sustainable sourcing. We are committed to doing this by ensuring that we become a Net Zero company by 2050. We look to deliver more sustainable approaches to benefit both our industry and the wider society.
Reach the World. Giving Made Easy with Impact.
Amelia Inskipp
Related Articles
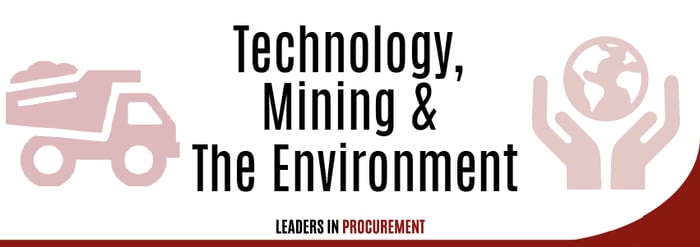
Tips & Tricks
Technology, Mining and the impact on the environment
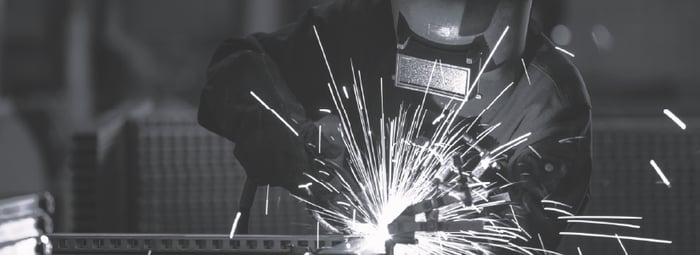
Tips & Tricks
Technology and Mining Safety
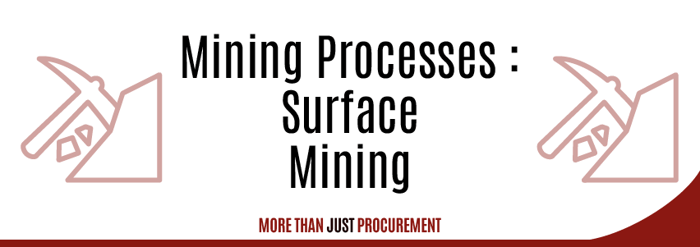
Business News
Mining Processes: Surface Mining
Don't Miss Out On A Thing
Sign up and Join Our Newsletter Today